Propulsion Lead
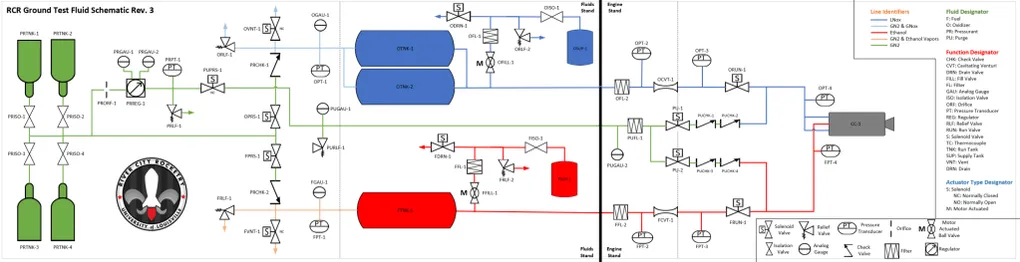
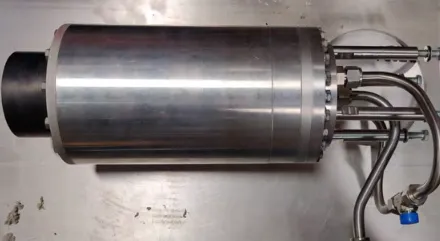
Top: P&ID for our planned kerolox, 1000lbf, 700psi Pc, N2 pressed engine. Bottom: Combustion chamber for previously (no longer) planned 1000lbf ethanol/nitrous engine.
Related posts: On my rocket team I also built somerockets of my own, and captained the team.
I have been the lead of my rocket team’s propulsion subteam since September 2020. My subteam usually had between 5 and 10 members. I inherited an ethanol/nitrous engine. We decided to switch to kerosene/LOX in early 2022 because of more member and advisor experience with LOX than nitrous, kerolox being more industry-applicable, and still being able to use most of our existing hardware after switching.
As propulsion lead, I taught all parts of propulsion design to team members, including fluid systems, combustion, cooling, component selection, P&ID design, and various aspects of safety. I communicated frequently with our team’s liquid propulsion advisor and various university contacts including safety professionals and university leadership (for funding). I oversaw the creation of an entirely new feed system P&ID (pictured above), lead the team through a propellant switch, and largely decided the direction of the team.
We have yet to hot-fire anything, but we have less of a “paper engine” than many propulsion teams. We have a mostly completed test stand (red weldment pictured above) and already have most of the components in the above P&ID in hand. However, we’ve also been beset by funding and bureaucratic issues, as well as the obvious COVID, otherwise we would have been able to hot-fire years ago (our liquids team was started around 2018, a year before I joined the team). To get past these issues, we decided in January 2023 to focus on a ~10lb thrust engine to be used in the future as an igniter for our main engine, to raise funds, build member experience, and showcase safe rocket engine operation. We are also working on a custom engine simulation program capable of simulating regen cooling, and with an iterative solver to determine optimal design conditions (wall thicknesses, cooling channel geometry, size, and number) for a given variable (like coolant temperature at exit from cooling channel).
Most of the skills I possess, technical and communicative, were first developed on the propulsion team. Through my time as a member and lead, I’ve learned a truly indescribable amount about liquid rocket engines and everything surrounding them (DAQ/control systems, fluid systems, test stands, safety), and just as much about the arts of leadership, effective task delegation, member mentorship, and good ol’ clear, concise communication.
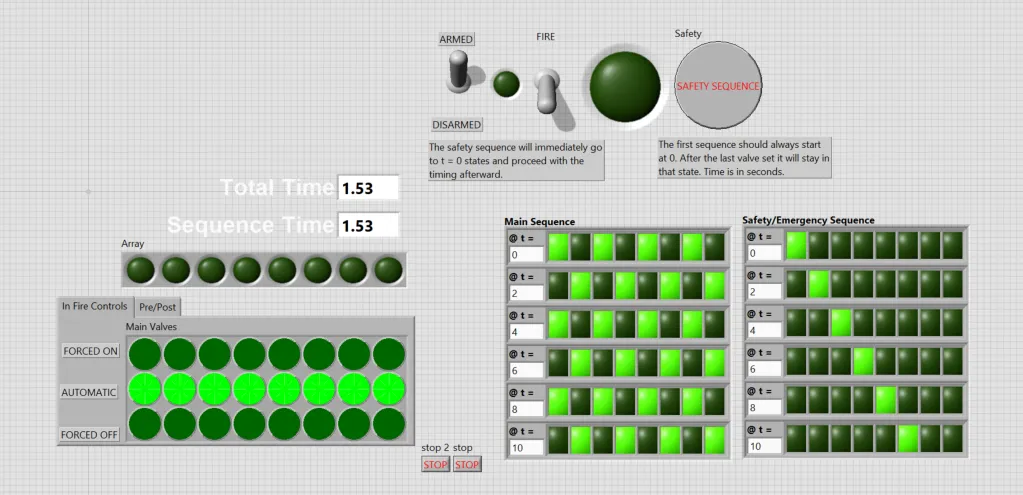
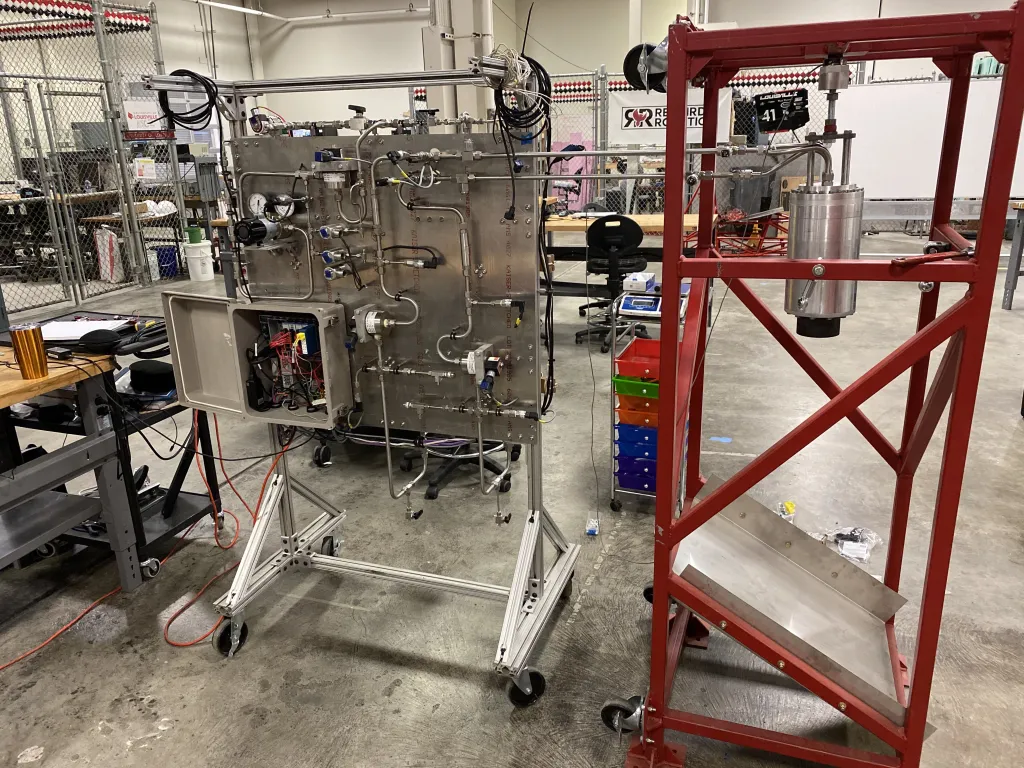
Top: Control panel built in LabVIEW for the pictured feed system. Bottom: Most of the team’s ground hardware, which was initially built for above pictured engine.